Complete mastery from R&D to the finishing touches
Know-how and innovations
For more than 30 years, Incidence Sails has been a reference in offshore racing and also among all major shipyards. As the First French sailmaker, Incidence Sails is born of the combined talents of passionate sailors. It is today, a group that hires and innovates.
In its premises, at sea or behind computers using High-tech software systems, the Incidence Team is a real expert and always highly committed.
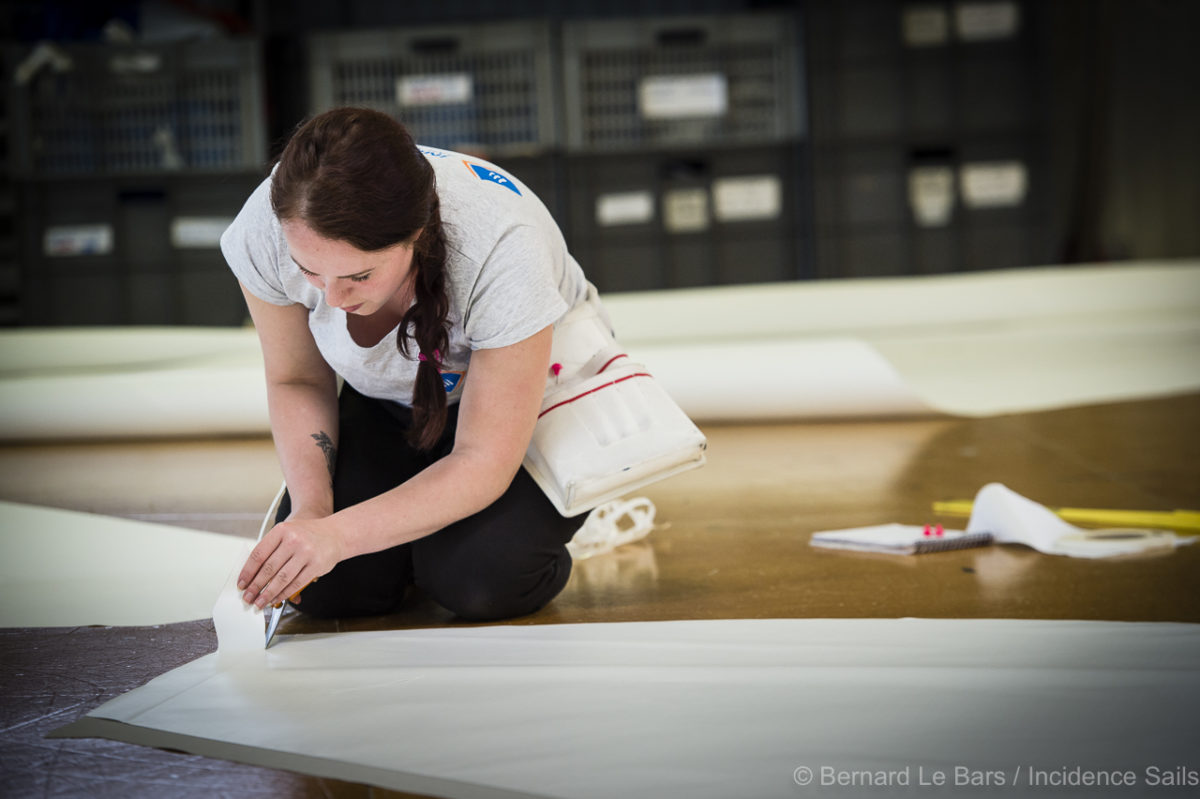
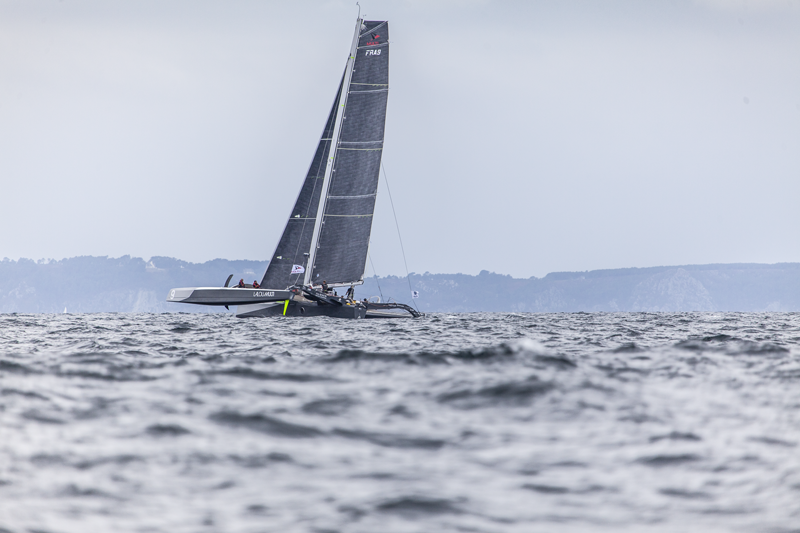
1st French Sailmaker
- Incidence Sails is one of the only two sailmakers in the world to make its own filament membranes, the DFI® and the DFI FIT®.
- An Outstanding track record: Vendée Globe, Jules Verne, records, Route du Rhum, Solitaire du Figaro… growing stronger every year.
- Strong lasting partnerships based on the sails’ reliance and quality and an outstanding service, involved in the largest shipyards (CNB, Fountaine Pajot, Lagoon…) and with new generation manufacturers (IDB Marine, MMW…).
- In 2020, a new sail-loft in La Rochelle will be opening just beside the Incidence Technologies production site. A new offshore racing center will also be opening in Lorient La Base.
- Another Innovation for 2020.
What makes our strength and our difference is our entire control, internally, of each step in a sail design. From R&D to finishings: this is “homemade” work carried out by our experts.
Confident and satisfied racers
Sébastien Simon, Skipper of the Arkea Paprec IMOCA. “In terms of performance, I have no doubt on the quality of the profiles, I’m totally confident and have no concern at all. The profiles fall perfectly. Nothing to complain about.
There’s been no going back to the floor. This saved us a huge amount of time.
The sails made of DFi FIT® are light. The Frac and Code 0 manufactured last year for the Route du Rhum (that equipped the former PRB of Vincent Riou, ed) in DFi® have aged very well.
Exchanges with Maxime Paul are always meaningful and the sail loft is always ready to make efforts on deadlines, even in tight timing. This is a great asset for us.”
Gildas Mahé (Breizh Cola / EquiThé) 2nd on the Solitaire Urgo Le Figaro: “I am very satisfied with my sails. Maxime Paul and Ronan Floch have done a great job during the development phase: there is no performance gaps. The results of the Solitaire du Figaro speak for themselves.
I’ve had no reliability issue. The sail-loft is not known for decreasing grammage to gain on weight. These are very well-finished and robust sails. Everything is spotless, the sails haven’t moved.”
Tom Laperche (Bretagne CMB Espoir) equipped with a Mainsail in D4, 4st on the Ocean Racing French Championship Elite, 2nd rookie: “I am happy, I’ve been one of the fastest of the fleet throughout the season. The Incidence foresails clearly have something more.”
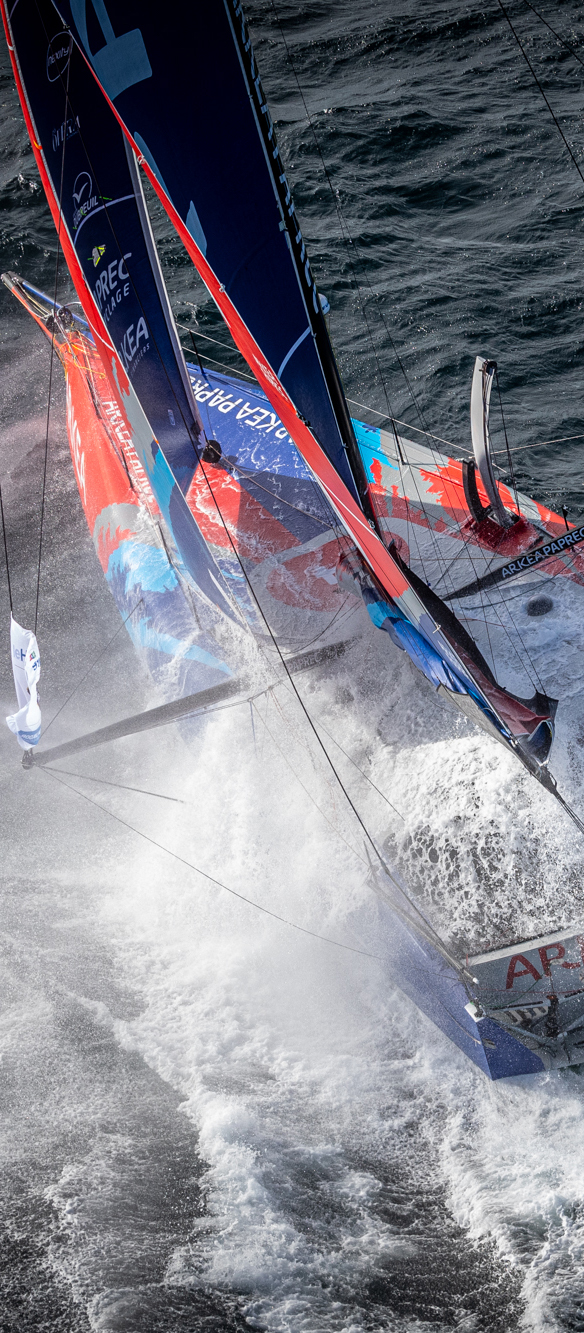
30 years and still in development
Nineties
birth and rise of a reference
1988
Sailmaking Incidence is created by a merger of “Voile Système” in La Rochelle and “Voiles Cudennec” in Brest.
Incidence established itself as the French leader in racing as in cruising.
Years 2000
Victories and Recognition
Incidence’s track record expands and the company gets into the circle of the most renown sailmakers in the world.
Opening of the floors on the Mediterranean Sea (2003) and in Lorient (2006).
Years 2010
Technology Supports Expertise
2013
Purchase of the “D4” production unit. Incidence becomes the 1st French sailmaker to manufacture its own membranes and to establish a design office dedicated to their development: “Incidence Technologies”.
2015
launch of the DFI® at the Nautic. Incidence is the second sailmaker in the world to gain access to filamentary technology.
2016/2018
Success of the DFI®, tested and adopted by racers, shipowners and shipyards. DFi® scores its first podiums in Ocean Racing: avec notamment 3 victoires sur la Route du Rhum.
2018 : lancement du DFI FIT®. Incidence est la voilerie la plus plébiscitée par les Figaristes. Le DFi FIT® adopté par le Team Arkéa Paprec, Lalou Multi…
2019
launch of the Strong luff.
2020
A year of transition: new sail lofts in La Rochelle and Lorient, investments at Incidence Technologies, intensified R&D, and further development of the DFi®
The investments made since 2013 become successful. Incidence becomes a major European stakeholder. The company acquired the resources for its dynamism et continues its development.
Incidence in numbers
Achievements
4 victories in the Vendée Globe
6 Jules Verne Trophies
6 victories in the Route du Rhum
2 around the world records, 9 Atlantic records, 3 24h records, 3 Mediterranean records…
12 victories in the Transat Jacques Vabre
7 victories in the Solitaire du Figaro
5 victories in the Mini Transat
Behind the scenes on how a sail is built
Behind the scenes on how a sail is built
At Incidence Sails, everything is designed, built, finished, and internally monitored in France. Nothing is outsourced.
Whether it’s for a production boat or a racing boat, each stage of the design and construction of a sail is “handmade” and monitored on the group’s premises.
A dozen different skills are put into the design of a sail, from a number of complementary professions, all of them creative and constantly evolving thanks to new software, modern materials and the ever increasing demands of master sail makers, as well as the sailors themselves.
« Every team and each individual person takes responsibility; and there is an interaction between the teams, this is why it works well. »
1. Definition of the specifications
The sail-makers’ sales team is comprised of sailors from the racing and offshore worlds.
Through listening to the boat -owner, the racer, the traveller, or the person who sails for pleasure, they will use their all their expertise to understand what they want, and to offer them the most suitable sail for their needs and to suit their budget.
They will then accompany the project until the first sea trials, and through any subsequent adjustments.
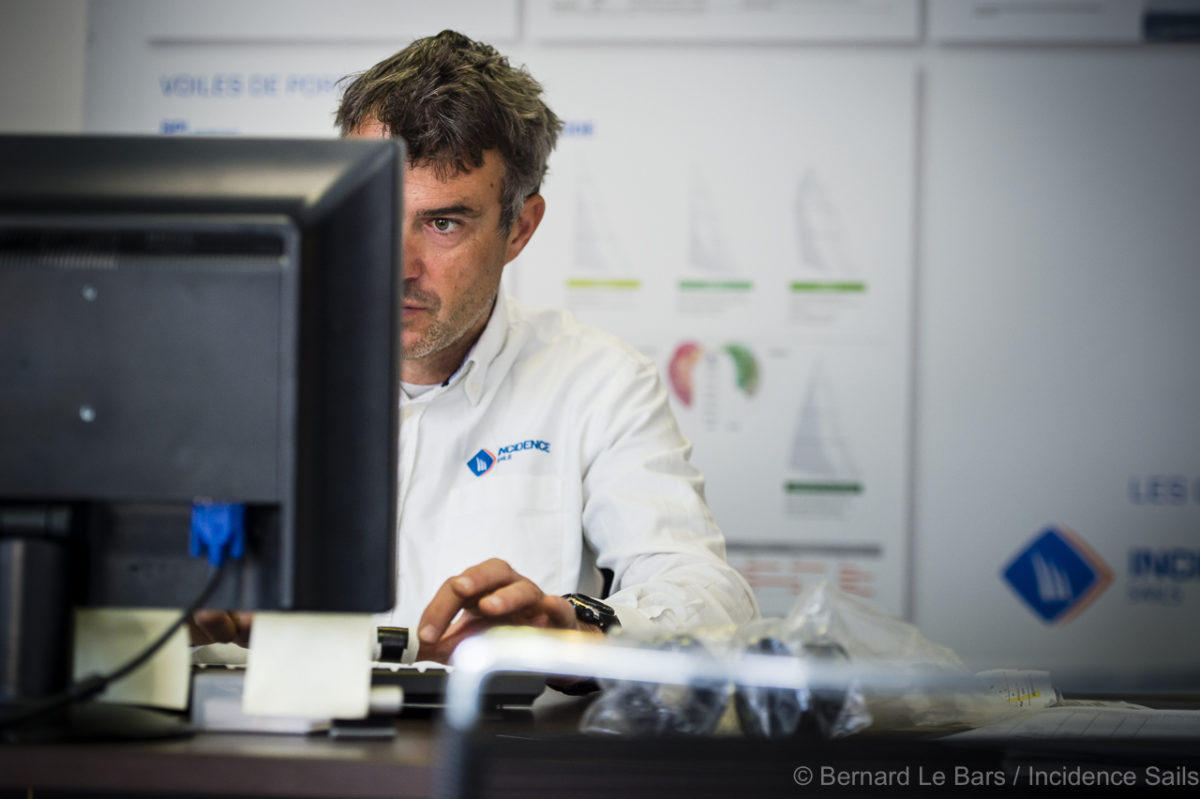
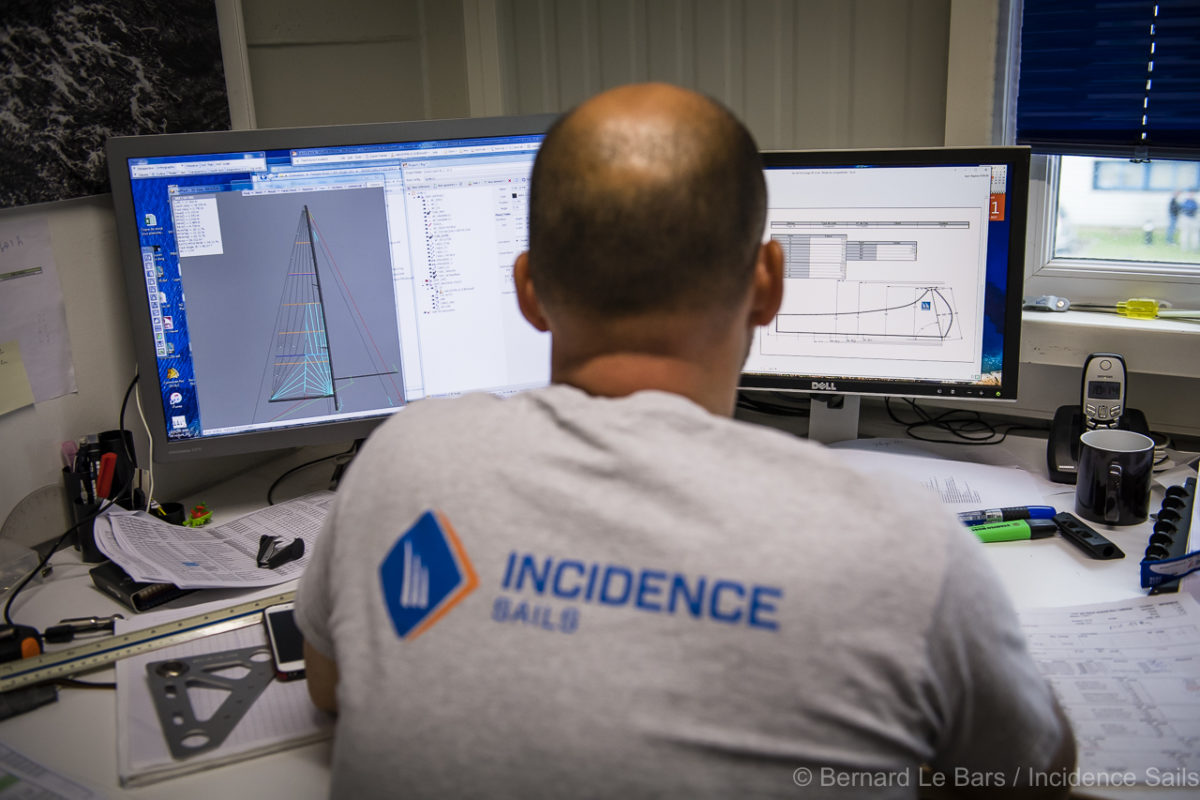
- Design
The Incidence Group has three design offices in La Rochelle, Brest and in Périgny for Incidence Technology. The designers, all of whom are sailors and yachtsmen, design sails on specialist computer software.
They make studies, calculations, and virtual designs for the sails on-site, so they can design, work on and refine the cut and reinforcements, and define which materials to use, depending on the specifications provided to them.
Once all of these elements have been determined, they create a “sail form”; a roadmap of the various stages of sail construction that lists the specific materials needed, as well as the design of all panels, measurements, the clamps, the reinforcements, the accessories … everything is included.
- Supply of Fabric
One person per production site is in charge of the supply of fabrics. At the end of the production line, each batch of fabric is tested by the producer, who then provides a graph of the resistance of each batch.
This information will help optimize the use of these rolls of fabric: they will only be used for sails where the specification requires these technical features. If the resistance is not satisfactory, a batch can be refused.
For membranes, the Incidence Group production sites are supplied with D4 and DFi® by Incidence Technologies. These membranes are used to custom-make sails according to requirements.
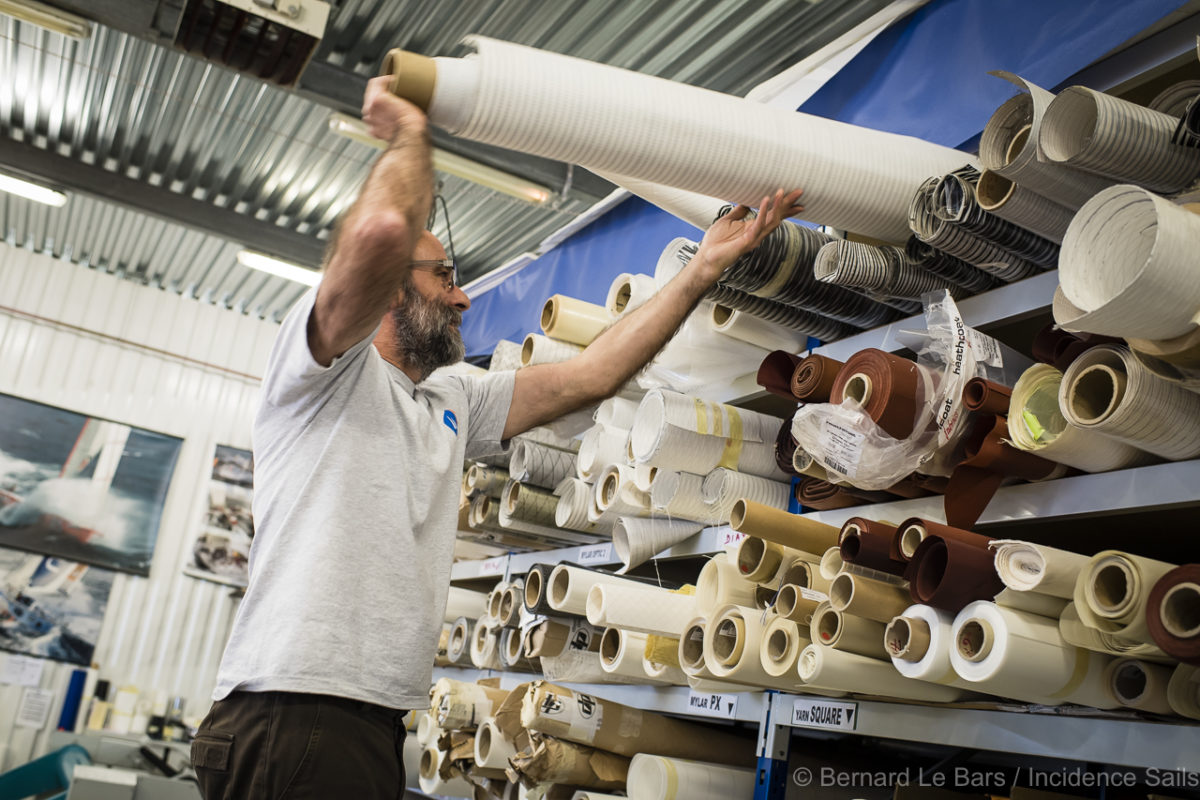
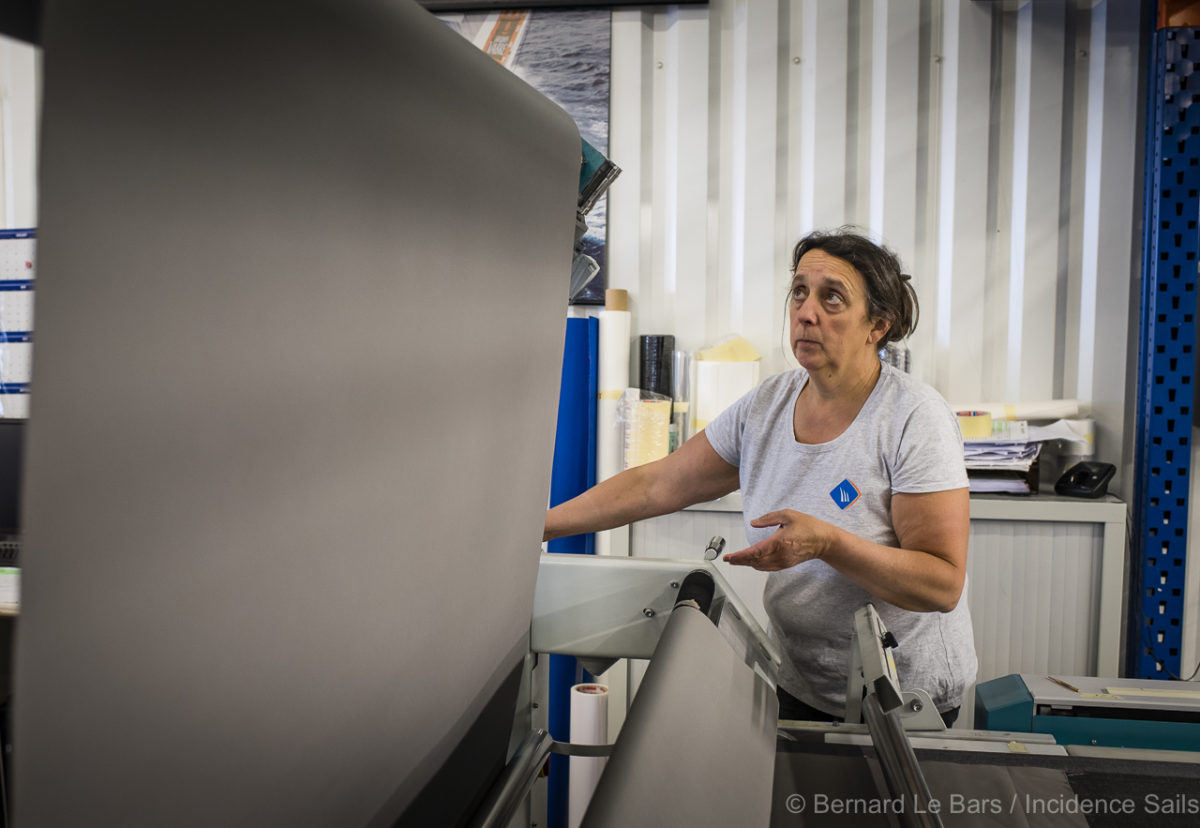
- Cutting
From the “sail form” provided by the designers, the lengths are positioned on the fabric roll in a way that fully optimizes the used of the material.
The cutting machine is a quality, French-brand machine, with a maintenance service and with reactive troubleshooting. Each of Incidence’s production units produces 80 to 100 sails each month. The machine provides the “raw material” directly for 35 people, so it is critical that it doesn’t break down, and if it does, then, only for a short time…
- Assembly
Each employee brings a different skill to assembling the sails. Some sail-makers specialize in the assembly of spinnakers. To do this, it is a veritable jigsaw puzzle with the materials. They scrupulously follow the plan provided by the designers, piece by piece. It could require anything from some hours to several days to put together a spinnaker, depending on the size and complexity of the design.
Others prefer to work on small sails, and in Brest, there is “Madame Figaro,” while the most physically strenuous work (by men or women) is assembling the large sails.
Experience and concentration are a must for sail making. It is not possible to pin them, and even if the pre-assembly of spinnakers can be done with tape, it’s necessary to place the panels perfectly as and when the machine stitches them.
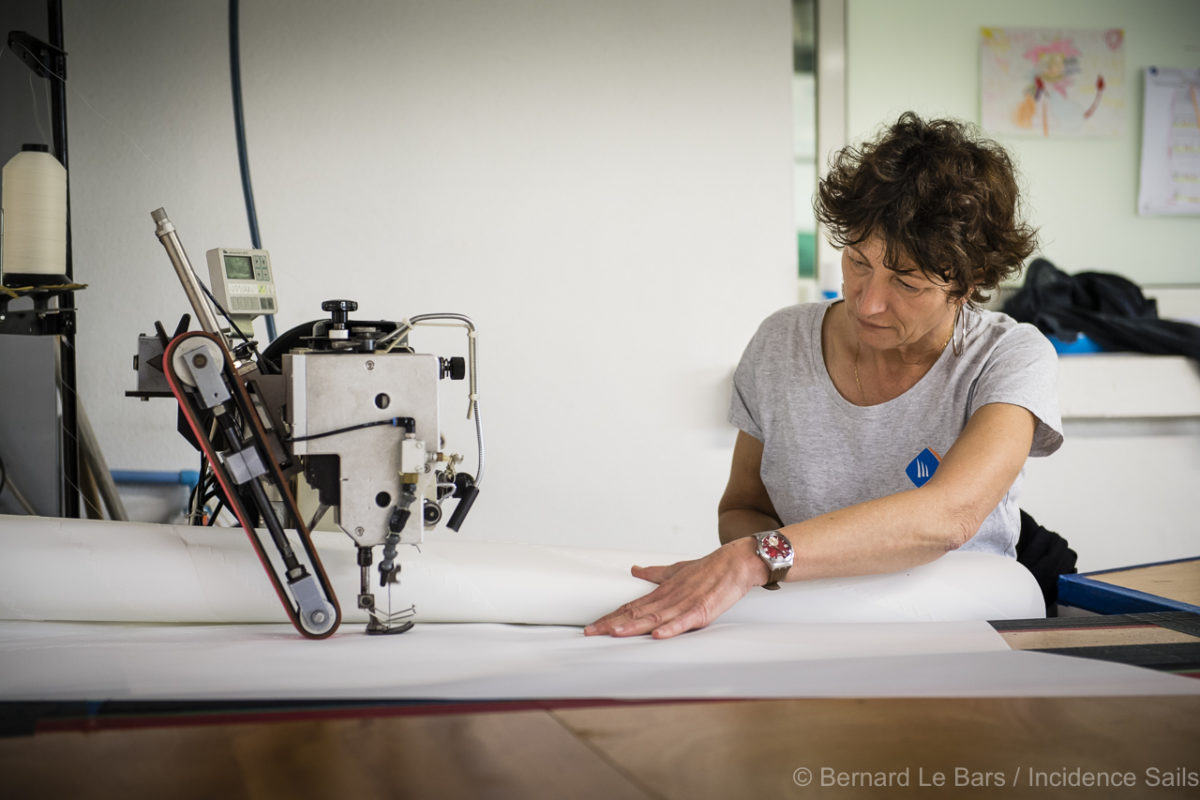
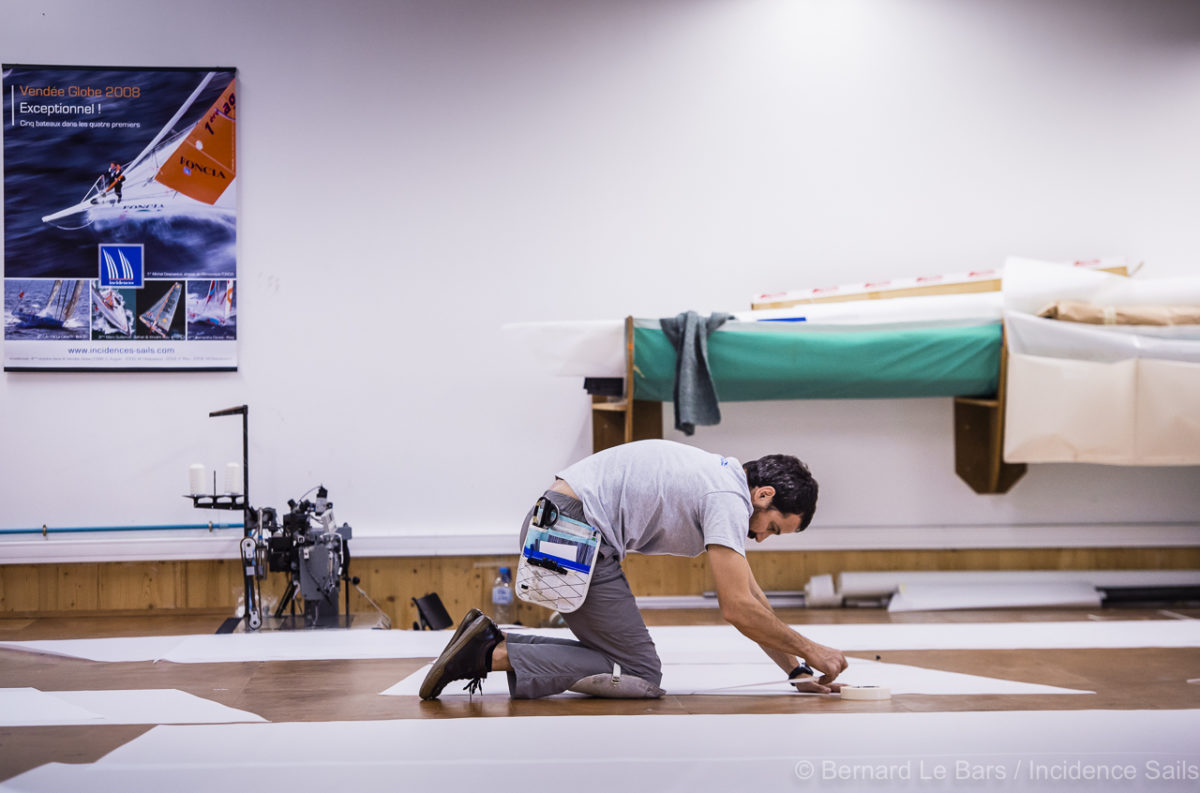
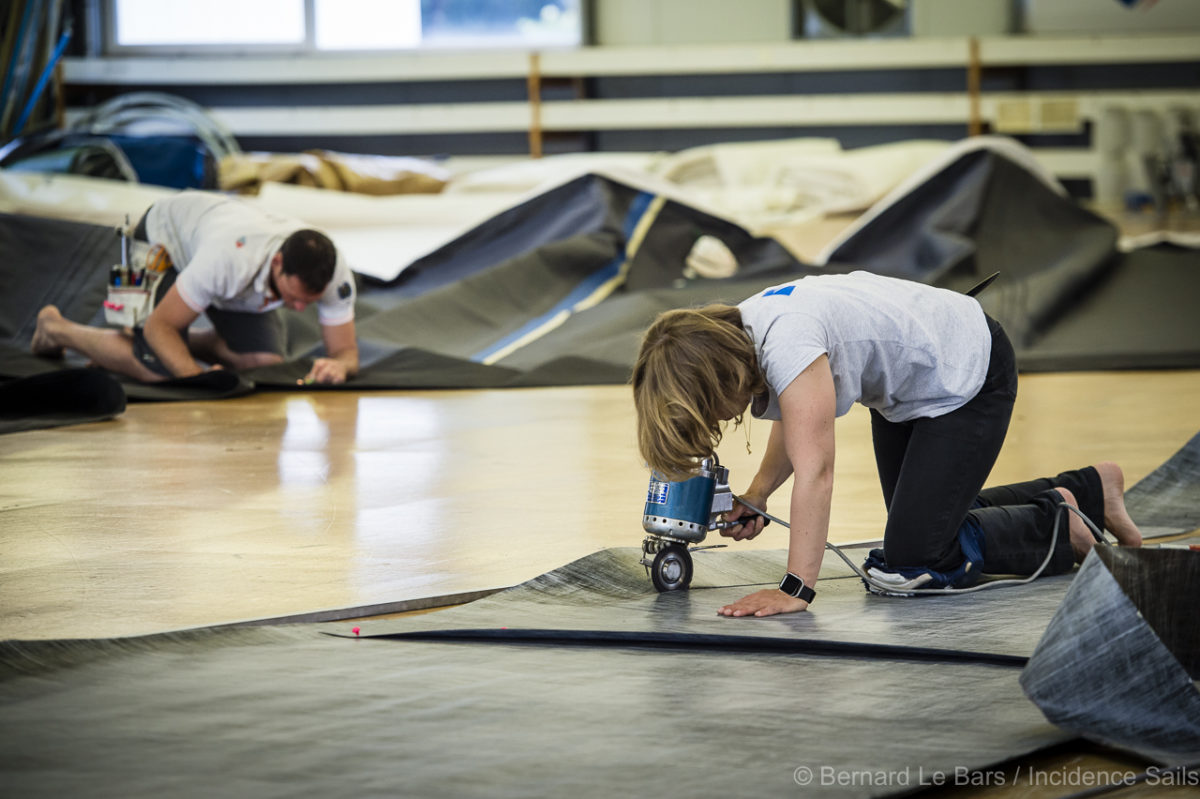
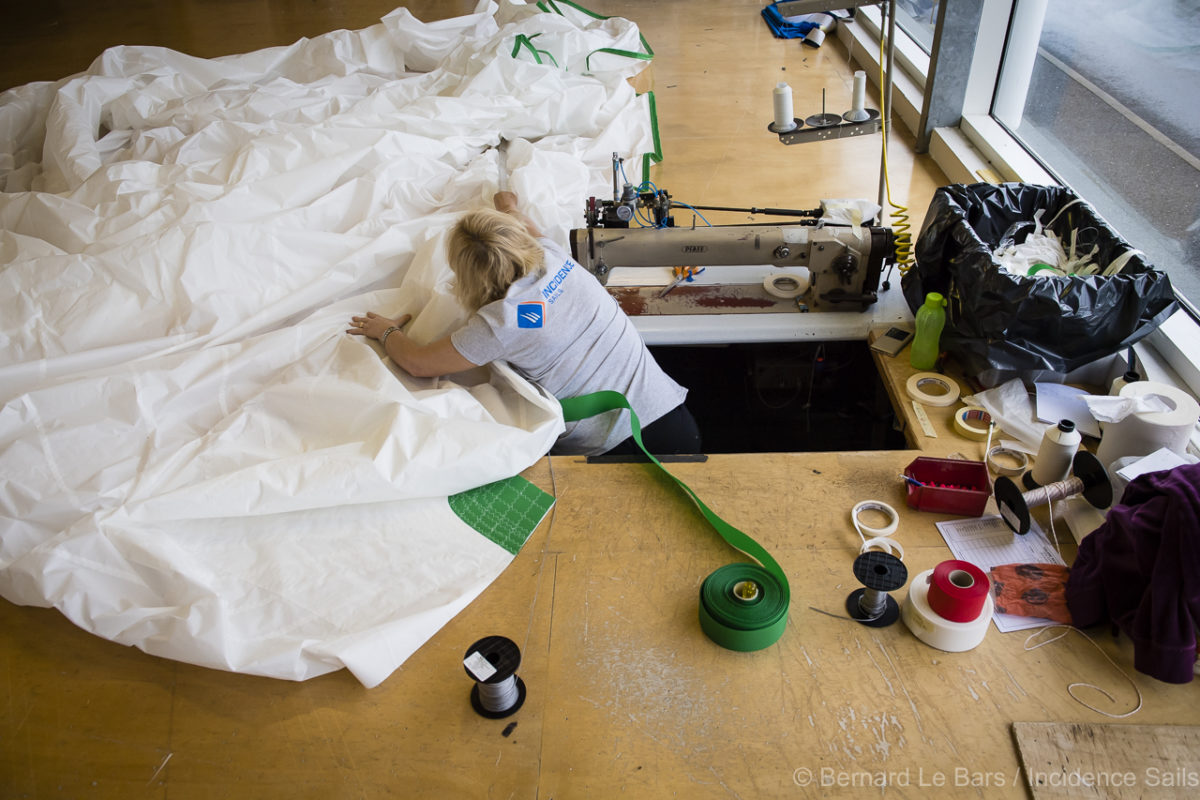
The work is varied and specific at the same time: with the one objective of creating a sail.
« Each sail is different. I like the diversity in this job. »
« We need to plan, and to adapt the work to each model. »
« I just put spinnakers together, it’s so colourful! I love doing it! »
« I specialise in assembling small sails and in particular, the sails for Figaro Bénéteau: this is a very demanding piece of work, I love the challenge and it motivates me! »
« I like working on small sails because the work is detailed and interesting. »
- Preparation
There is a strong team working on “the preparation.” So, for each sail, it’s necessary to prepare something known as “a case”.
It contains all the reinforcements, fittings, straps, tapes, daisies, and batten pockets necessary for a sail. For each boat, this could take anything from 2 hours to some days.
At the boatyard workshops, a template file is prepared and validated, following a careful system. With requests for specific custom-designs and for racing boats, the preparation team, in close dialogue with the research department, researches, innovates, tests, refines … to achieve the optimal custom piece.
The custom parts that are developed are stored in the “template file” to be used again when similar situations arise or as a basis for reflection to adapt to a new challenge.
« The work is constantly evolving! It is a creative art, and it’s interesting. »
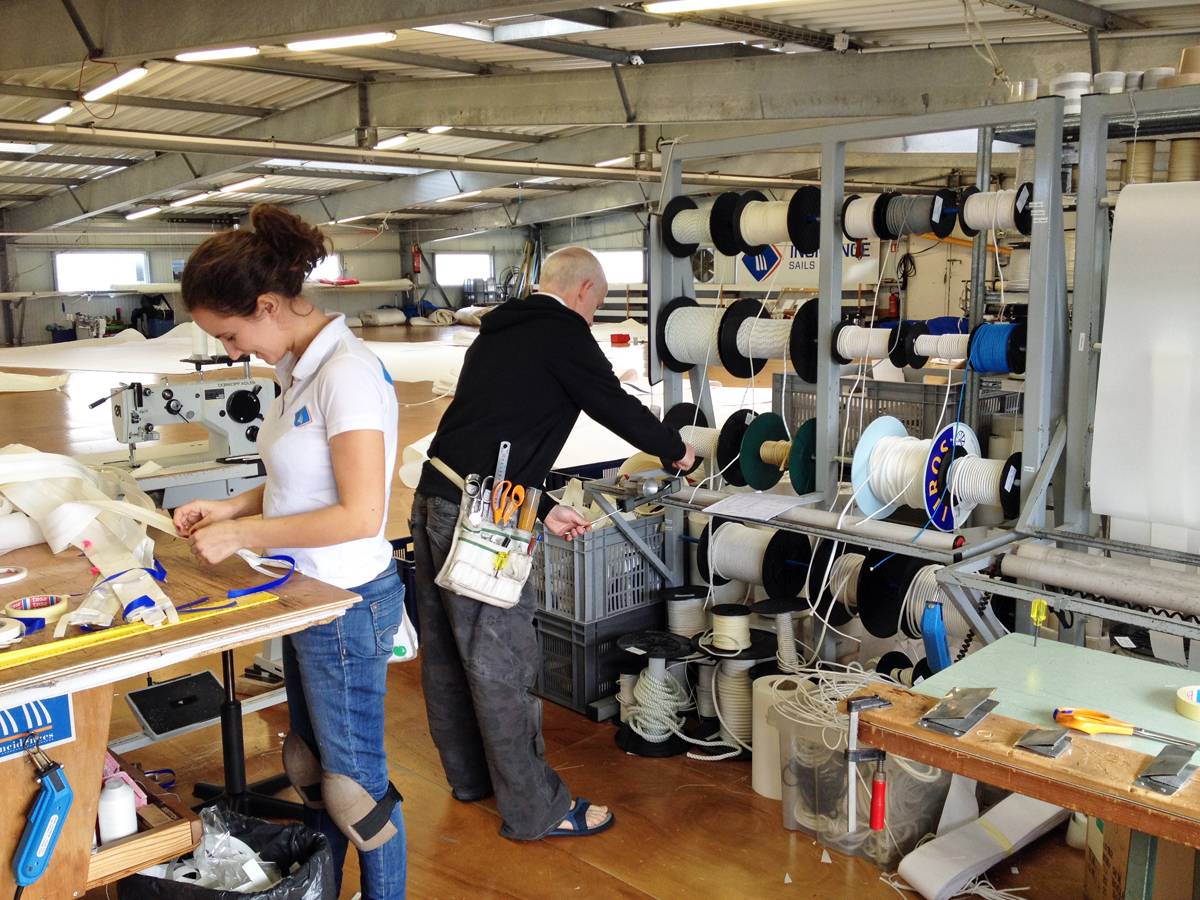
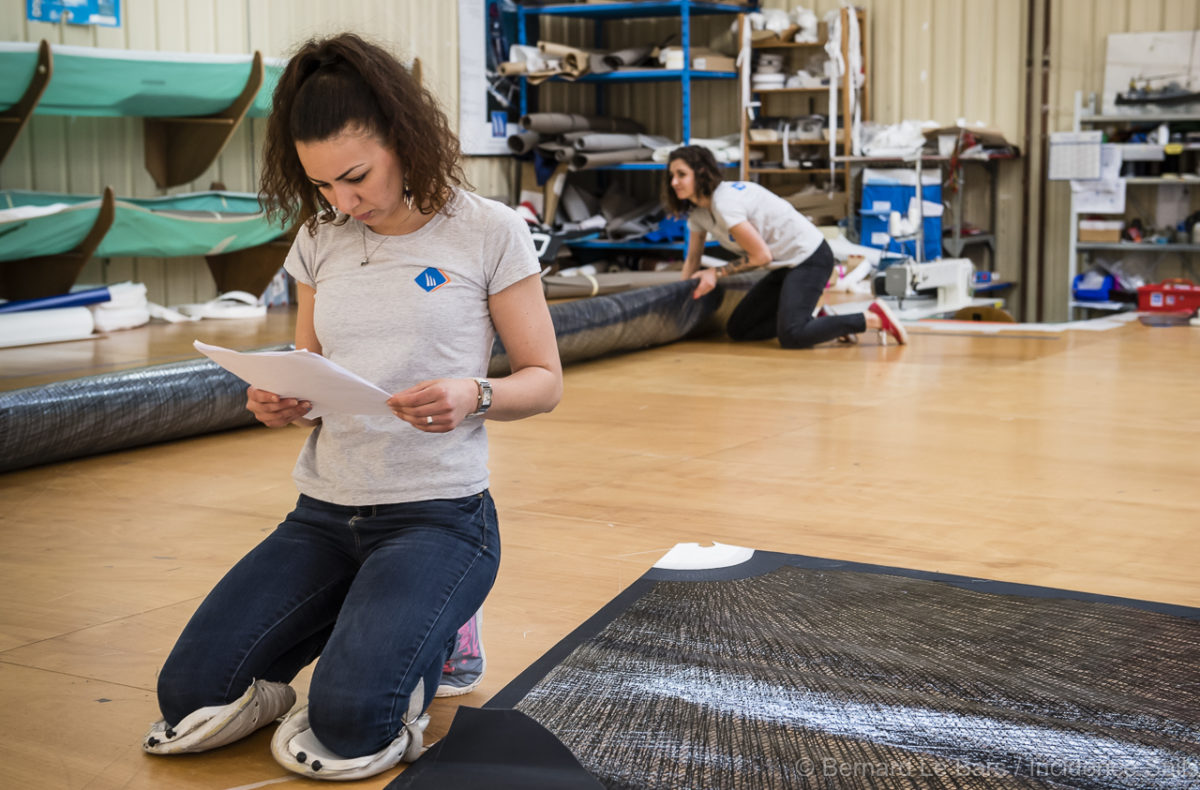
- Finishes
This is the part where they stitch together all of the accessories from “the case” (eyelets, straps, strips, housing, reinforcements…) for the sail. It takes about 6 hours for a series boat, and, for example, 20 hours for an IMOCA 60.
As in the other stages of sail construction, the team’s roadmap is the ‘’template form’’ made by the designer, but creativity is also essential. This profession is constantly changing; there is a constant search for the best weight and reliability. For racing boats as well as for production boats, they need to be aware of new materials and develop new techniques to meet changing requirements.
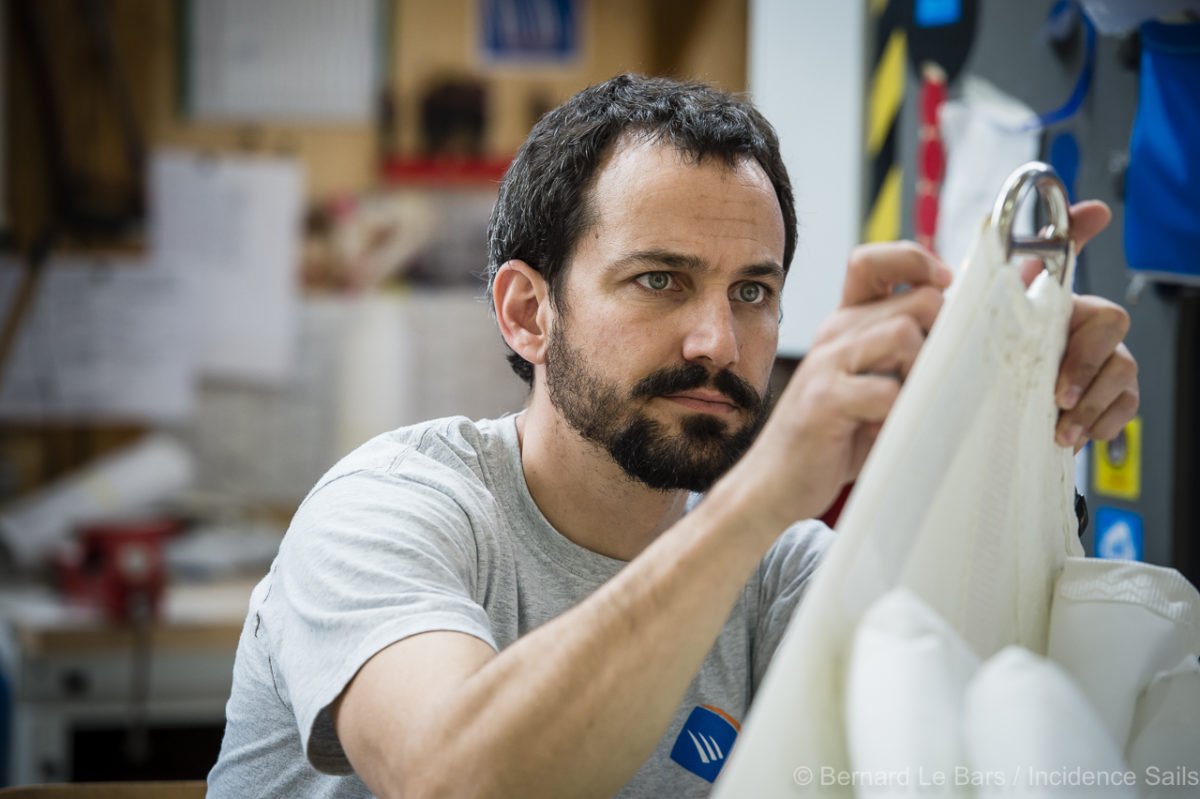
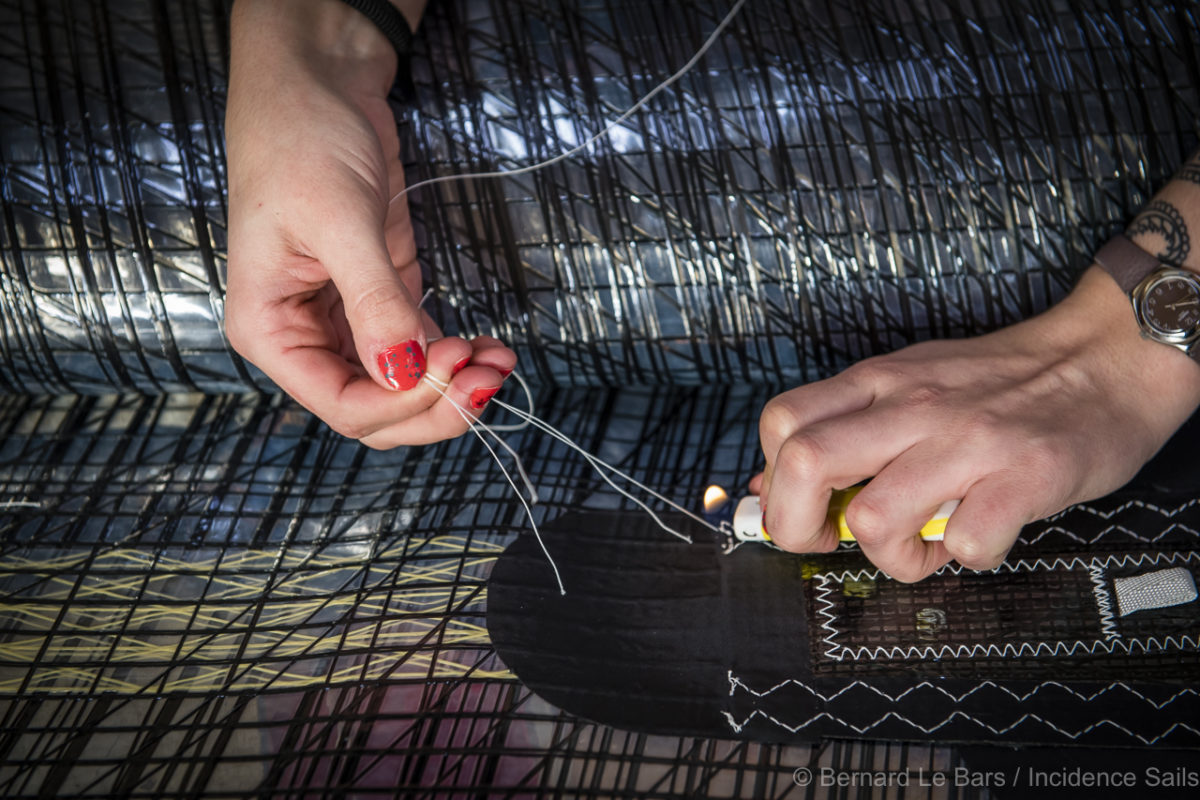
Incidence is one of the few sail-makers in France to not have outsourced the finishes on its sails: a guarantee of quality, creativity and responsiveness.
« The work is not monotonous and it’s always a pleasure working on the sails. » « I hand stitch … I check the finishes. »
« Je fais les points à la main… je vérifie les finitions. »
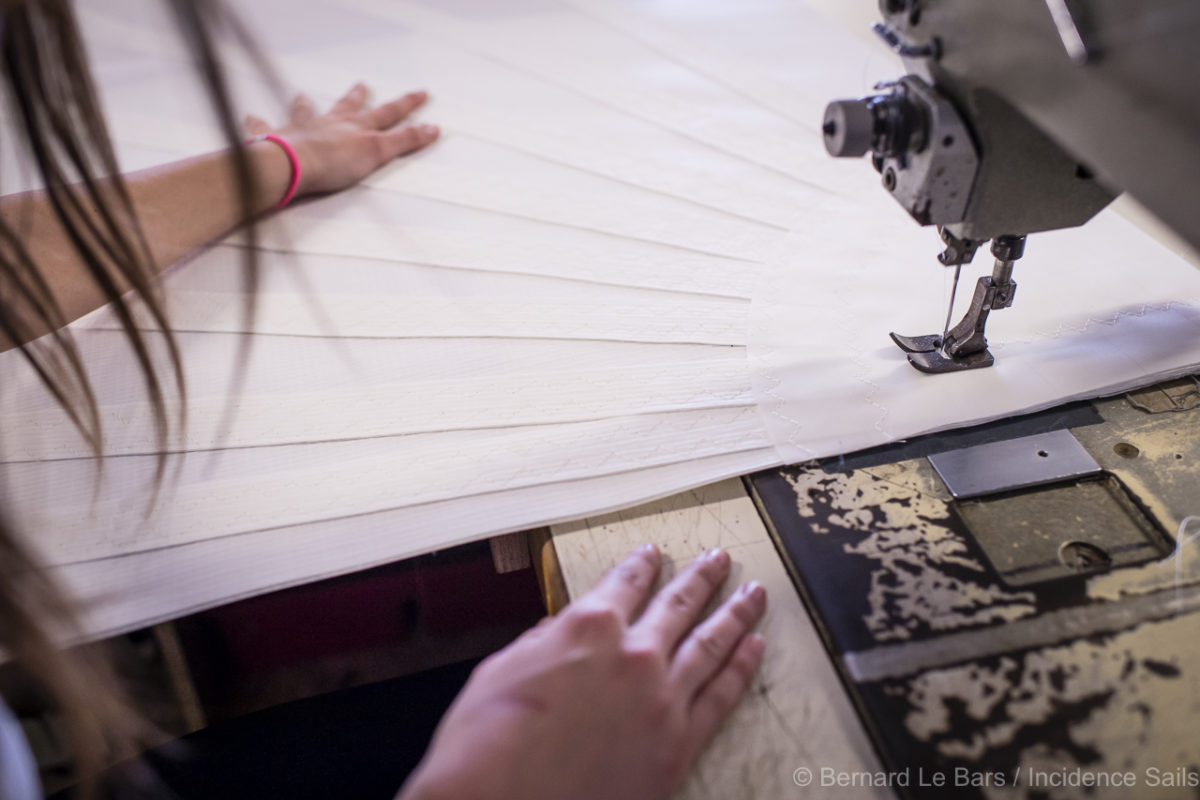
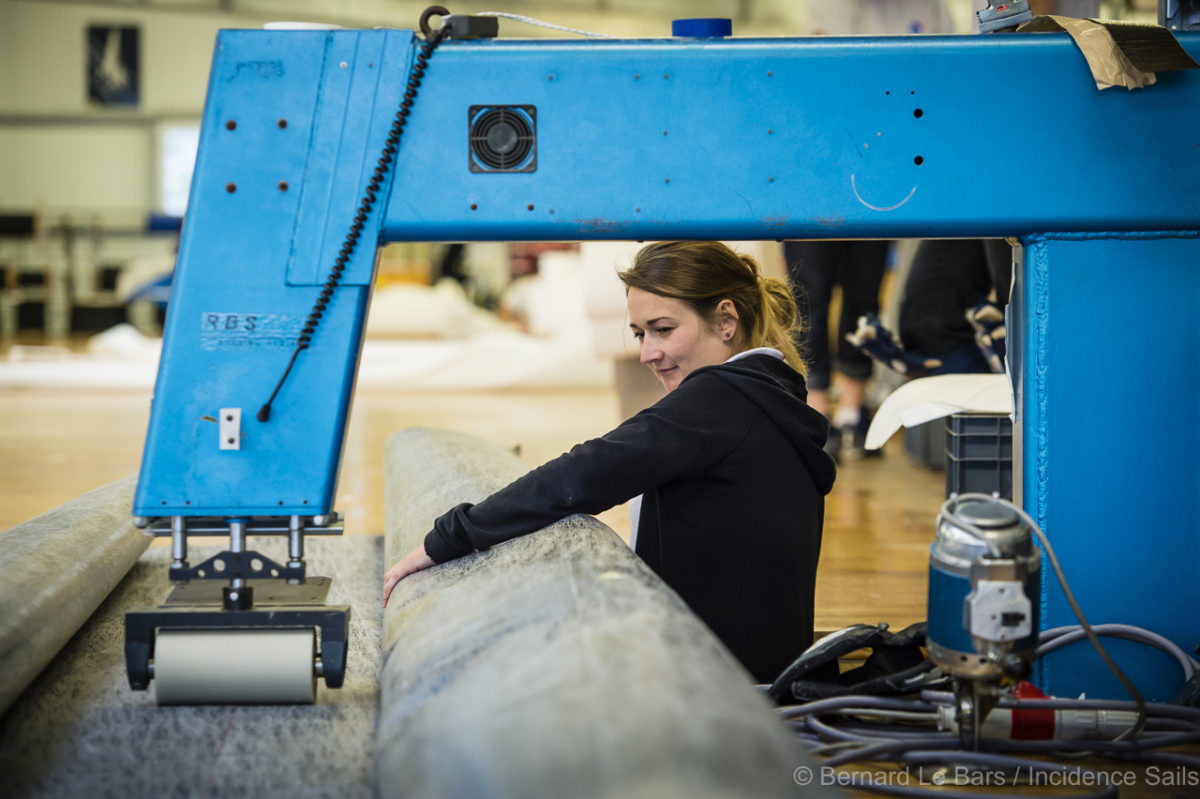
8. Bonding and head ropes
For large sails and membrane sails, the panels are not stitched; they are bonded. There is no room for even the slightest mistake in this precision work, which will give the sail its final shape.
The bonding is carried out mostly on rigid materials, on large panels, which are difficult to handle.
The edges are then adjusted and the head ropes are attached.
« If the sail does not bond well, it will not work! This work has a lot of responsibility and pressure. »
9. Repairs and Alterations
A workshop for repairs and alterations supports all types of sails (classic yacht IMOCA 60, to monotypes, to sailing yachts…) and all types of work.
This support requires a good knowledge of fabrics and materials, the constraints of each type of boat and their respective needs. It also requires some knowledge of the different skills needed in sail-making to be able to grasp what work needs to be done overall.
For racing boats, specifically, any work on the finishes will be carried out in collaboration with the design office.
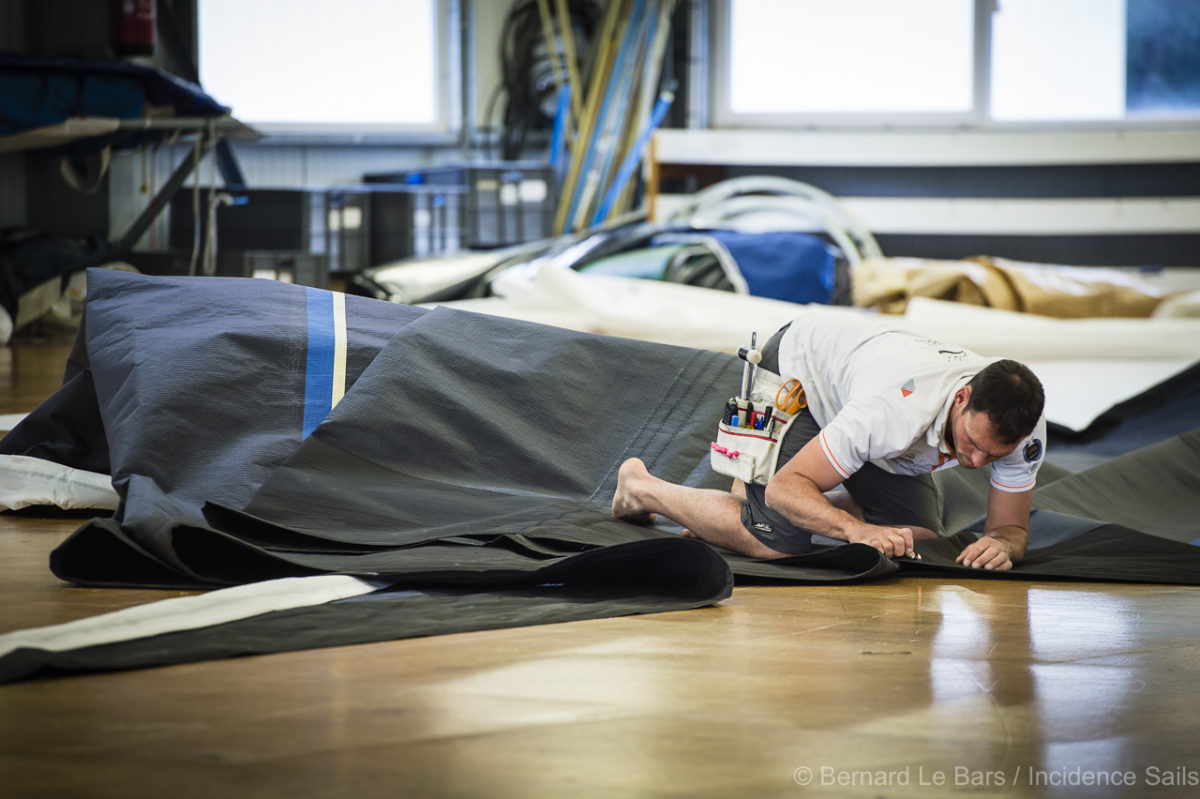
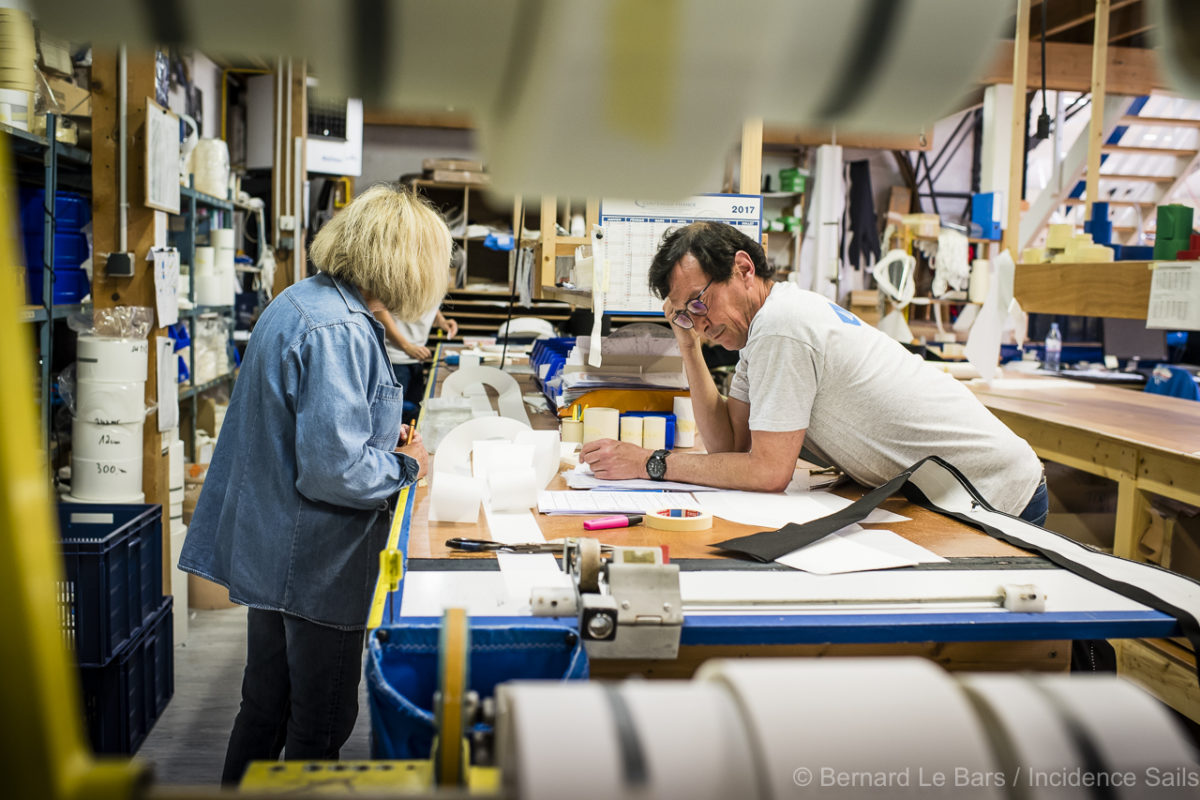
10. The workshop manager
A key figure on the ” workshop floor, he is responsible for starting the production and managing the workshop schedule of the teams. He also controls all of the sails, step by step (stitching, assembly, finishing), and ensures that they meet specifications.
He must know about all aspects of the sail, and have an overall view of work, with an eye on every detail…
« I have worked in all of the positions, starting with the finishes. I like everything about what I do! »
11. Bags and boat covers
The manufacture of standard sail bags is outsourced by Incidence (to rehabilitation workshops), but the sail bags for larger boats are made in-house, as well as the protective boat covers, called ‘ lazy-bags’.
In this case, as well, we need to be able to adapt, customize and invent …
« It’s great because it always requires a lot of thought in advance, in dialogue with the design office. »
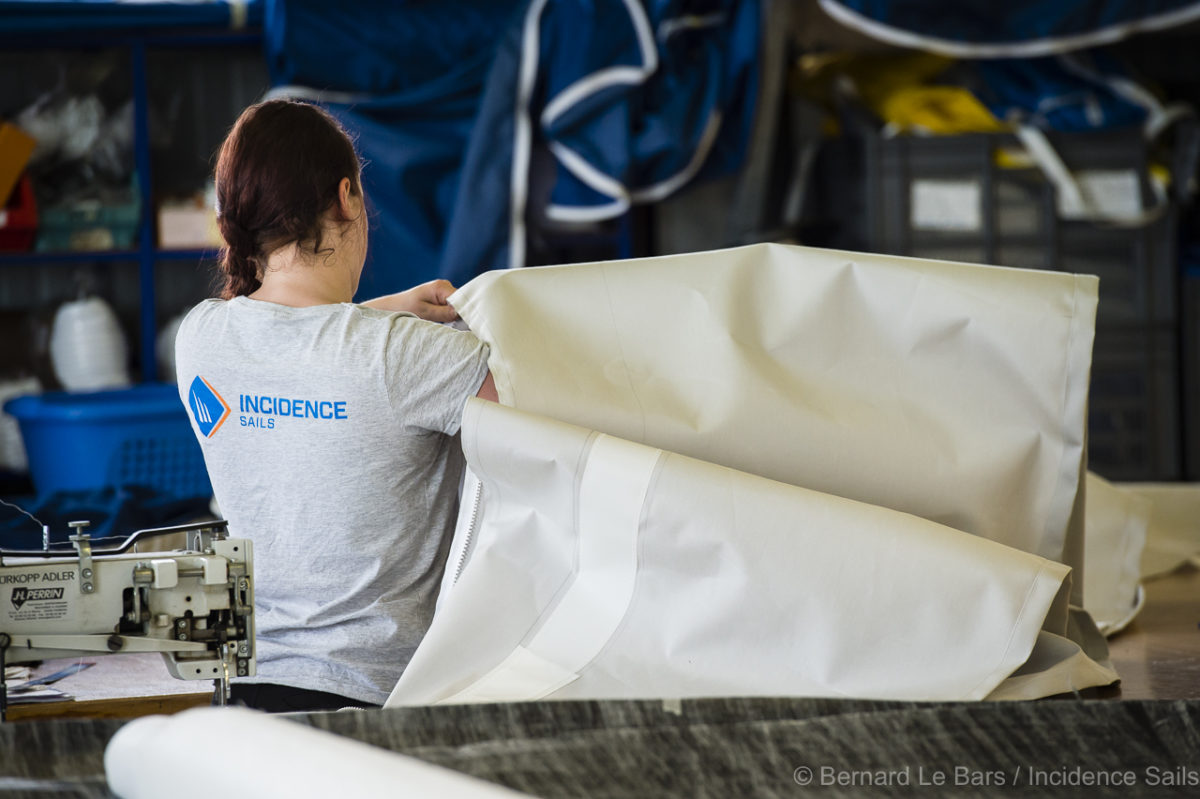
Set your sails well
Up wind sails
Headsails overview: their ranges of use according to the windspeed and wind directions…
- Code 0 : Between the lightweight Genoa and the asymmetric spinnaker, the range of use of the Code 0 goes from close hauled in light winds, to reaching in strong winds. When cruising in light to moderate conditions, the Code 0 generates a substantial gain making it an ideal replacement of the engine !
- Genoa: It is the most common and versatile head sail. Often rigged on a furler, it is used from 0 to 20 knots. Caution : when the genoa is partially furled, it loses performance because the remaining surface becomes considerably deep.
- Jib: small flat sail to use when the wind speed exceeds 20 knots.
- Heavy weather Jib: Small resistant flat sail in heavy fabric, to use when the wind speed exceeds 30 knots.
- Storm jib: very small flat sail, with a fluorescent orange color, hoisted when the safety of the boat is at sake, from 35 – 40 knots.
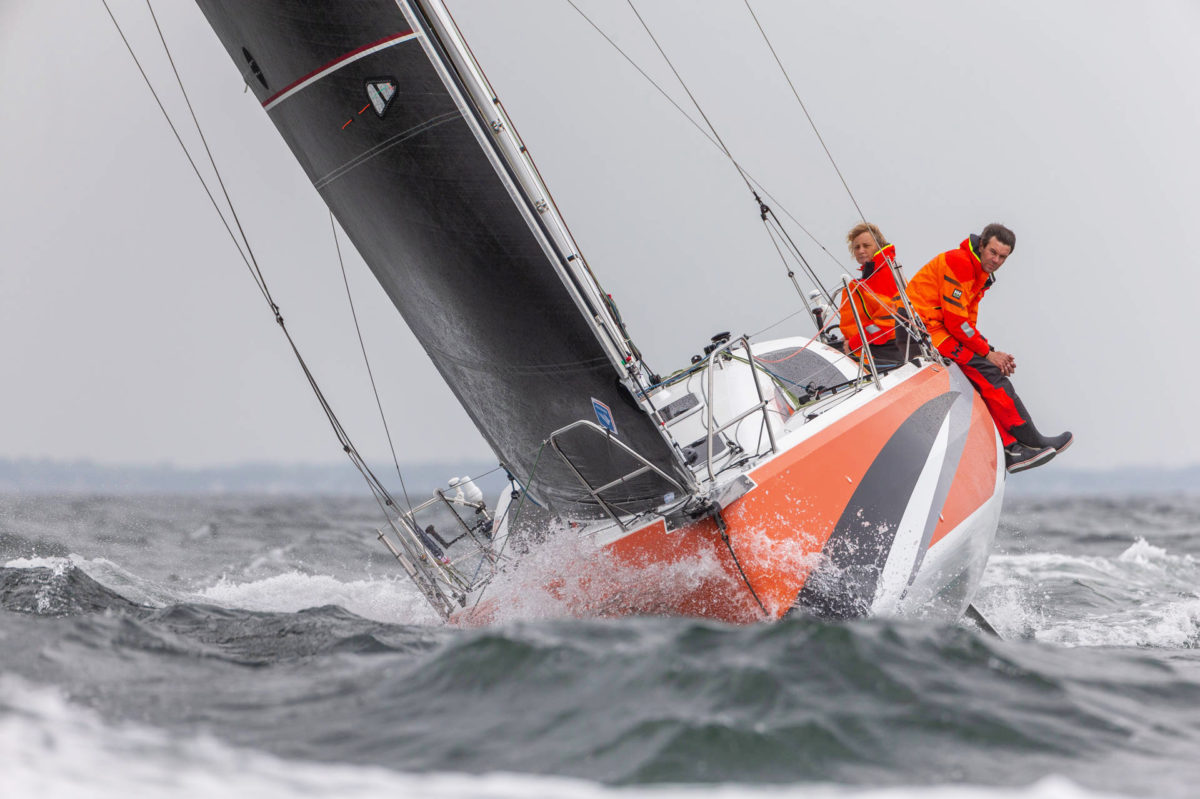
Downwind sails
- Gennaker : Very deep genoa used for reaching and downwind. Rigged on a furler, it is very simple to handle and is perfectly adapted to cruising as a spinnaker subsitute. The gennaker is used from 0 to 25-30 knots, it can have a medium to heavy weight depending on the navigation program.
- Symmetrical Spinnaker S2 : medium weight and multipurpoise downwind spinnaker,
- Symmetrical Spinnaker S3 : Heavy weight spinnaker adapted to higher angles in strong winds.
- Asymmetrical Spinnaker A2 : medium weight and versatile asymmetrical downwind Spinnaker,
- Asymmetrical Spinnaker A3 : Heavy weight spinnaker adapted to reaching in strong winds.
- Asymmetrical Spinnaker A4 : heavy weight downwind spinnaker adapted to sailing downwind in strong winds.
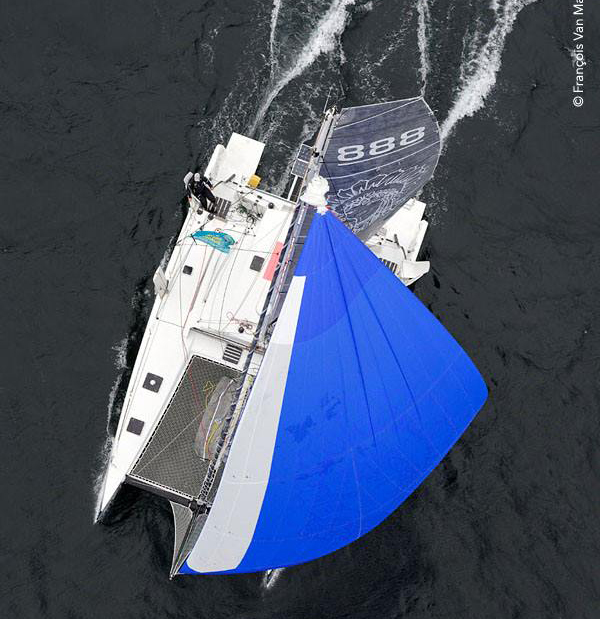
To each boat, its own sails
Monohulls (production)
Short distance cruising > Horizontal or radial cut sails made with Dacron or laminated materials.
Long distance cruising > Laminated sails or Hydranet (Polyester and composite fibres).
Racing/cruising > Laminated sails with taffeta protection, or laminated Pentex ( provides better shape than with polyester)
Racing boats
Lightweight sails (laminated or membrane) that stay in shape with a good stiffness and low stretch.
Cruising catamarans
Square top main sail in Hydranet (Polyester and composite fibres), for more power while cruising. In laminated or solid membrane for a gain in performance.
The good sail settings
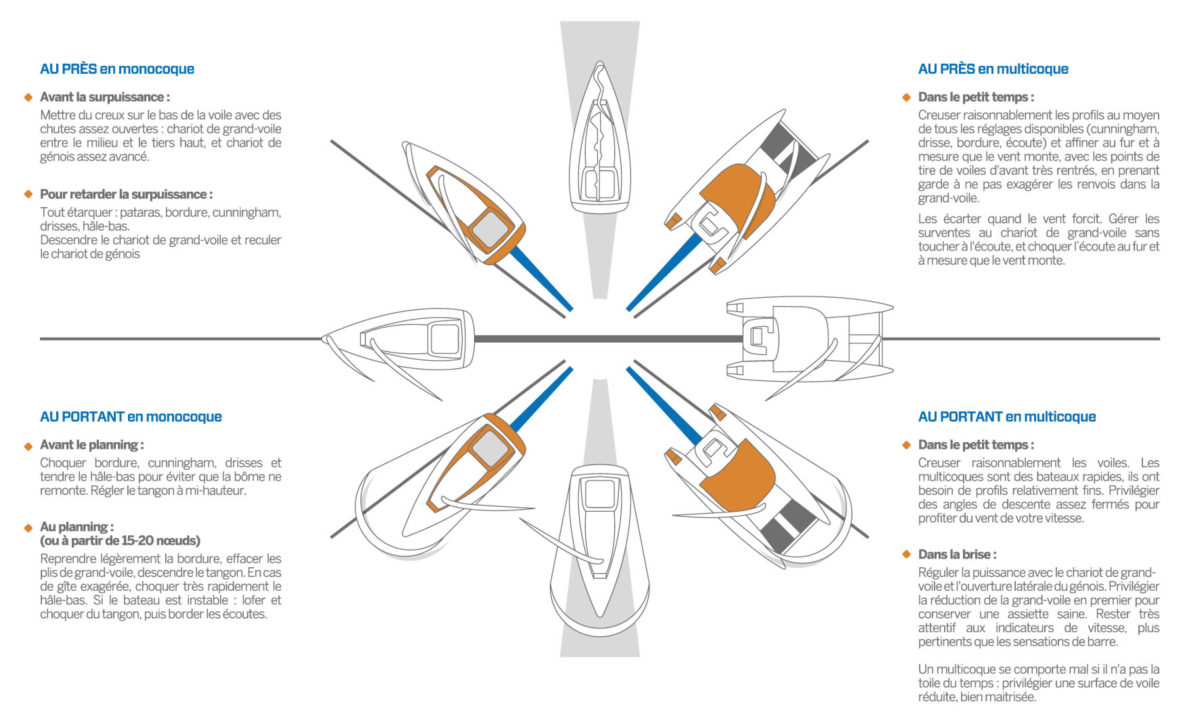
Sail maintenance
There is nothing difficult about taking care of your sails. A few precautions and good habits will help you to keep their shape, their look and to age without a wrinkle !
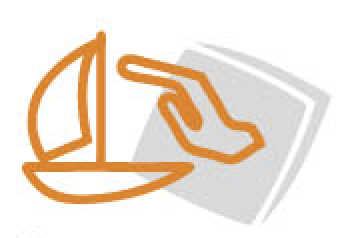
- Preparing
Prior to using your sail for the first time, identify each piece of deck hardware & rigging likely to damage it, and install the necessary protections (stanchions, cleats, spreaders, turnbuckles, etc.)
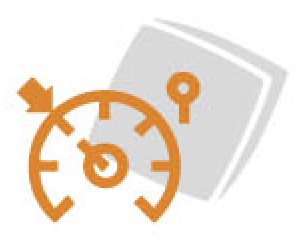
- Moderate and anticipate
During the first sea trials , avoid the windy conditions: favour medium wind to allow the fibers of the fabric to bed-in in a balanced way.
Avoid excessive tension (luff, foot, sail battens …) and limit the « flapping ». Improve durability by limiting sailing in over-power conditions, and take care not to exceed the range of use planned for your sail.
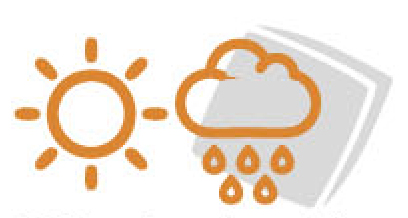
- Recovering and protecting
Back at the harbour, roll, fold, furl without crushing or over-tightening the fiber. Take care to protect your sail from sun radiation and bad weather (awning, bag, sock, lazy-bag, etc.).
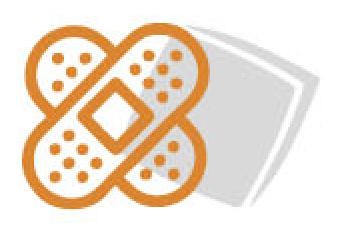
- Repair
Repair minor tears right away: many technical solutions and repair kits are available from all good shipchandlers. In any case, do not hesitate to contact us for advice or expert advice.
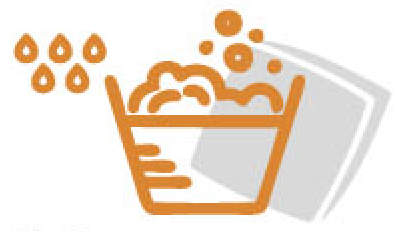
- Cleaning
We recommend regular rinsing with fresh water: the salt does not damage the sails, but it retains moisture and generates corrosion on metal accessories.
Stains of mold, rust, oil, blood, tar can be removed using suitable products available from shiphandlers, or in DIY stores.
For a complete wash, use a product with a neutral pH, and prefer a light and soft brushing.
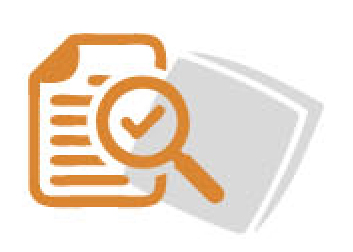
- Inspecting
The winter period is the ideal opportunity to thoroughly inspect your sail: check the seams, batten pockets, reinforcements, straps, leach line, etc.
Also, review the condition of your lazy-bag, spinnaker sock, awnings, deck bag …
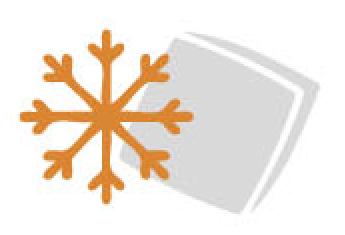
- Wintering
Ease-off the Leach line and foot, release the battens. (Tip: note down the battens tension to find the right setting for next season’s sailing.) Rinse your sail with fresh water, paying particular attention to the fittings such as eyelets, batten boxes, head plate, etc. Once the sail is completely dry, fold it or roll it up before storing in a clean, dry, ventilated place, away from UV and hot temperatures. Never winterize a wet sail.